Beanspruchungsanalyse von Kunststoffreibpaarungen in technischen Systemen als Grundlage der Versuchsplanung
3. Internationales GKT-Symposium
Kunststoffgleitketten und Tribologie in der Fördertechnik
Dipl.-Ing. Arndt Schumann
TriboPlast GmbH, Chemnitz
Modellversuche mit einfachen Probekörpern sind im Vergleich zu Betriebsversuchen des realen Systems weniger aufwändig und kostengünstig. In einem frühen Entwicklungsstadium reibungs- und verschleißbeanspruchter Kunststoffbauteile helfen Modellversuche, praxisnahe Versuchsergebnisse zu gewinnen und ermöglichen damit eine objektive Entscheidung bei der Kunststoffauswahl. Die Voraussetzungen dafür sind, dass die Versuchsparameter und der Versuchsaufbau des Modellversuchs mit der tribologischen Beanspruchung des realen Systems stimmig sind.
Der Beitrag zeigt, dass schon geringe Abweichung der Beanspruchung zu großen Unterschieden im Reibungs- und Verschleißverhalten von Kunststoffreibpaarungen führen. Deshalb ist es in Bezug auf die Verwertbarkeit der Modellversuchsergebnisse entscheidend, die Versuche auf der Basis einer umfassenden tribologischen Beanspruchungsanalyse zu planen.
1. Zusammenhang zwischen dem Beanspruchungskollektiv und dem tribologischen Verhalten
Bei der Neu- und Weiterentwicklung reibungs- und verschleißbeanspruchter Kunststoffbauteile bildet die Beanspruchungsanalyse der Reibpaarung die Grundlage für eine korrekte Kunststoffauswahl. Die Versuchsplanung basiert ebenfalls darauf.
Warum ist die Beanspruchungsanalyse so wichtig? Das Reibungs- und Verschleißverhalten von Kunststoffbauteilen ist eine Systemeigenschaft. Jede Änderung bereits einer Einflussgröße kann eine starke Erhöhung oder Reduzierung z.B. des Gleitreibungskoeffizient oder des Verschleißes bewirken.
Die Folgende Abbildung zeigt die Einflussfaktoren.
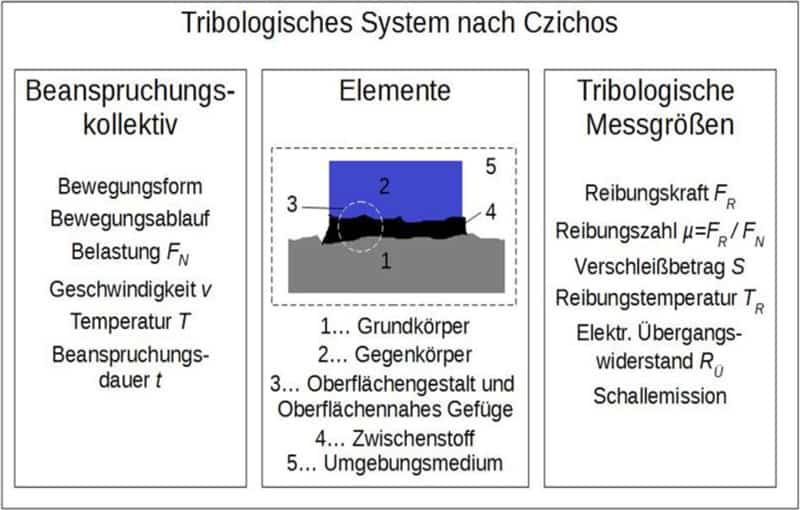
Die nachfolgenden Diagramme verdeutlichen die Abhängigkeit des Reibungs- und Verschleißverhaltens vom Belastungskollektiv.
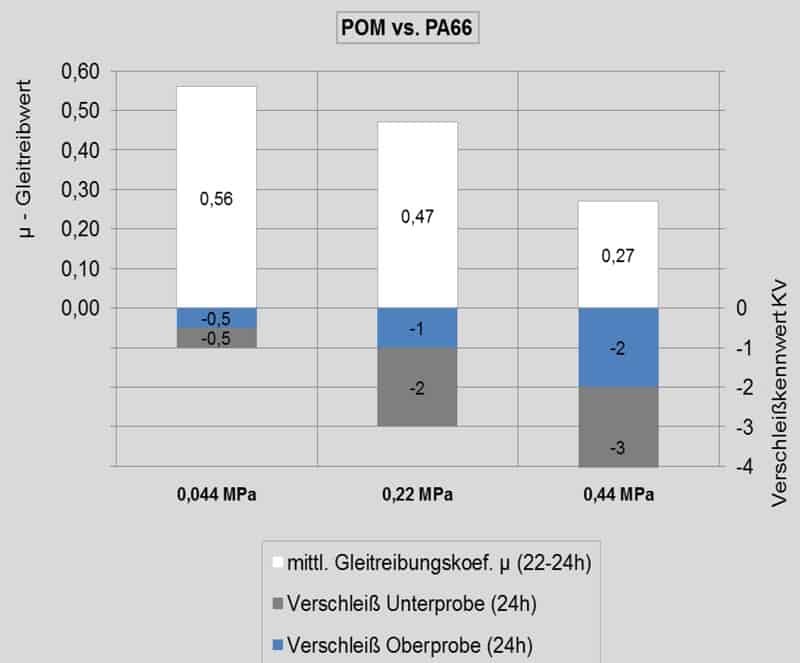
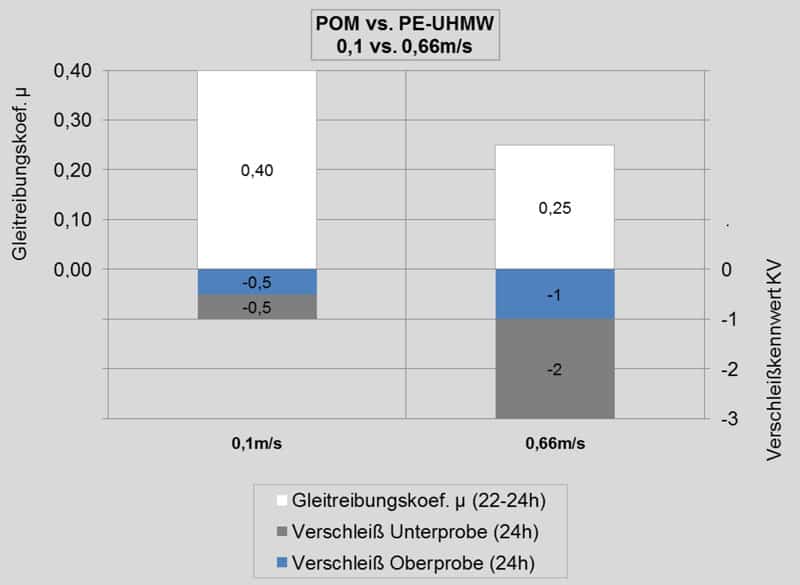
Die Oberflächengestalt und die Orientierung der geometrischen Formen zur Bewegungsrichtung bestimmen unter anderem die Kontaktverhältnisse und beeinflussen wesentlich das Reibungs- und Verschleißverhalten (Vgl. Abbildung 4; Abbildung 5; Abbildung 6). Stegstrukturen, wie in Abbildung 4 dargestellt, können auch aus der Fräsbearbeitung von Kunststoffoberflächen resultieren!
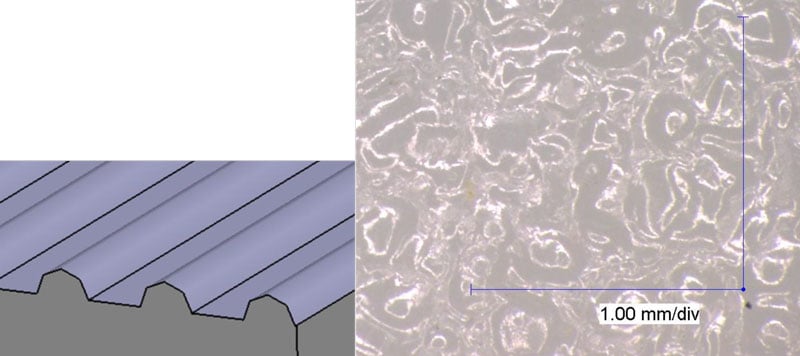
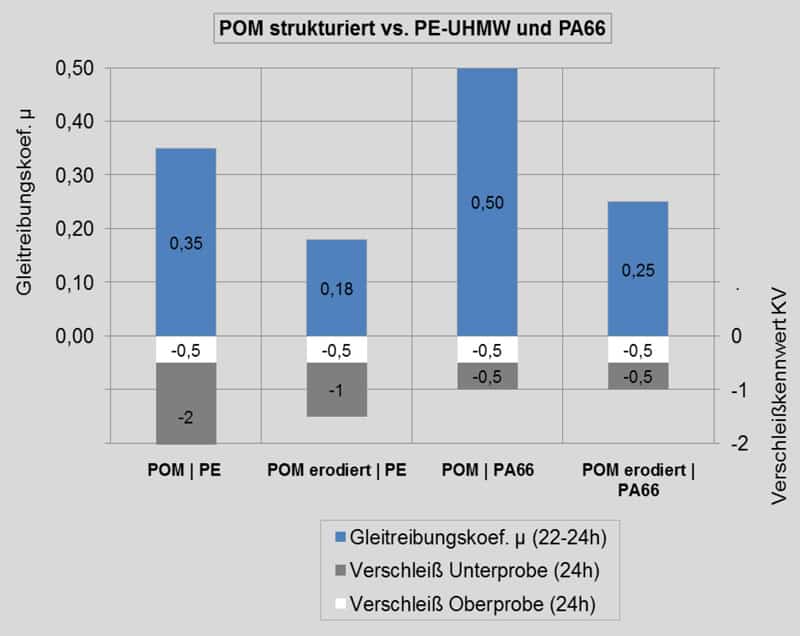
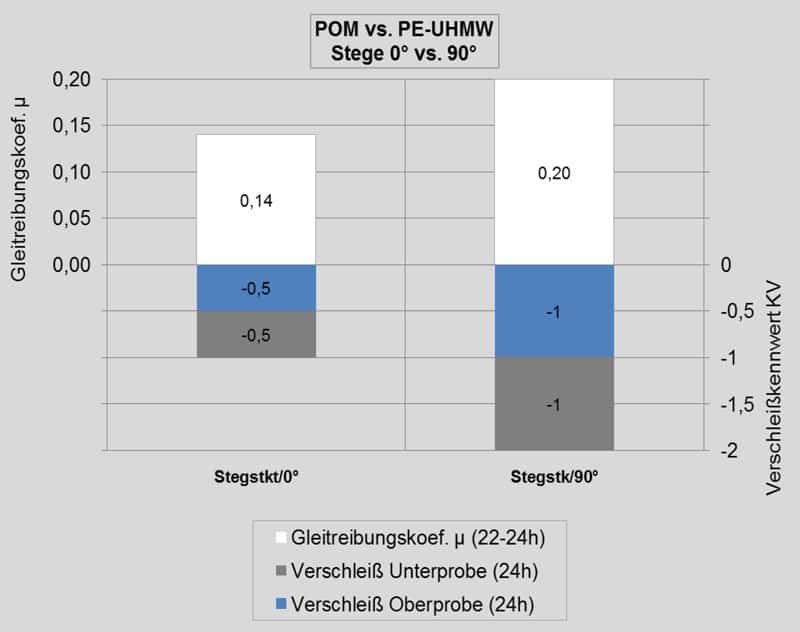
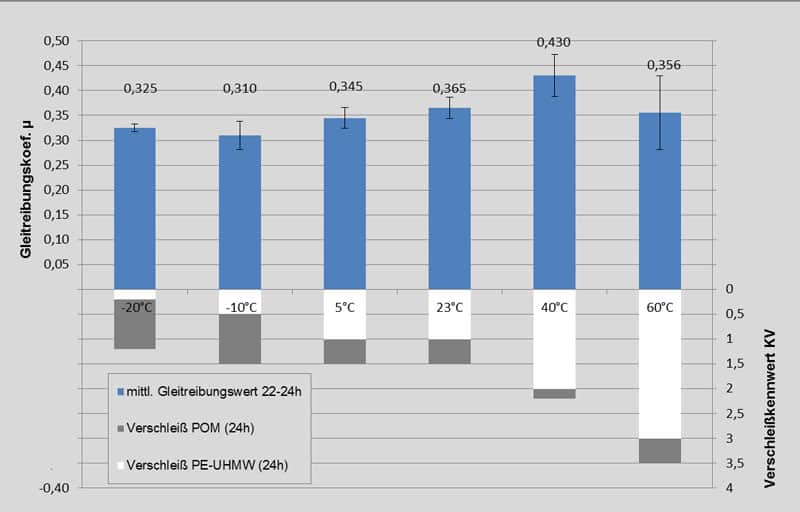
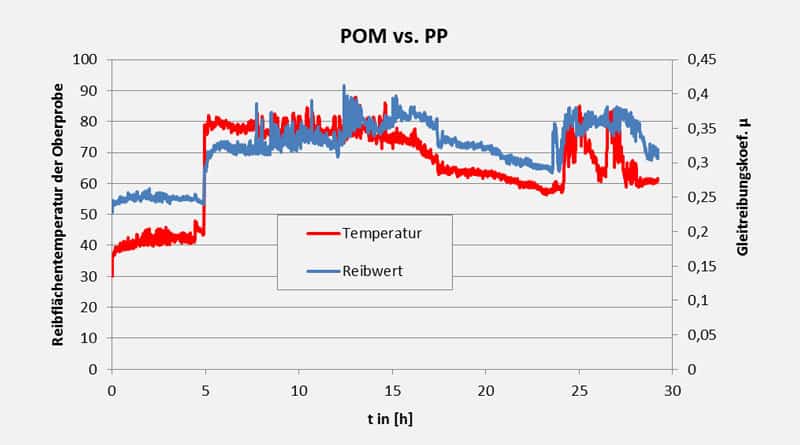
Die Entwicklung der Reibflächentemperatur wird unter anderem sehr stark durch die Größe der Kontaktfläche und die Wärmeisolierung des Reibkontaktes beeinflusst. Bei großen Kontakflächen oder Baugruppen, die den Reibkontakt gegen das Umgebungsmedium abschirmen, kann die Reibungswärme kaum abfließen. Die Temperatur im Reibkontakt steigt und wirkt sich auf den Reibungswert und den Verschleiß aus.
2. Die thermische Beanspruchung des Reibkontaktes ist der „Knackpunkt“!
Die Abbildung 7 und die Abbildung 8 zeigen sehr deutlich den Einfluss der Umgebungstemperatur und der Reibflächentemperatur auf das tribologische Verhalten. Im Vorfeld tribologischer Untersuchungen müssen die Ursachen für die thermische Beanspruchung sehr genau betrachtet werden, da bekanntermaßen bei Reibungsvorgänge Wärme entsteht und das mechanische Verhalten thermoplastischer Kunststoffe dadurch sehr stark beeinflusst wird. In diesem Zusammenhang sind alle Einflussfaktoren, die sich auf die Wärmeentwicklung im Reibkontakt auswirken genau zu analysieren.
Der Einfluss der Flächenbelastung, der Reibgeschwindigkeit, der Oberflächengestalt und der Oberflächenorientierung sowie der Temperatur wurden in den obigen Diagrammen dargestellt. Entscheident für die Entwicklung des Reibungswertes und des Verschleißes ist die Wirkungsdauer der Flächenbelastung, Reibgeschwindigkeit und Temperatur, und zwar separiert bezüglich des Grundkörpers und des Gegenkörpers.
Bei den meisten Reibpaarungen gibt es eine große Abweichung der Wirkungsdauer zwischen Grund- und Gegenkörper, diese Tatsache muss bei der Versuchsplanung und der Kunststoffauswahl berücksichtig werden.
3. Beanspruchungsanalyse am Beispiel der Reibpaarung Kettenglied – Gleitschiene in einem Fördersystem mit Kunststoffgleitkette
Die folgende Abbildung zeigt in der Seitenansicht einen geraden Streckenabschnitt eines Fördersystems mit Kunststoffgleitkette. Die Kettenglieder (2) bestehen aus einem Stück. Auf der Kette liegt das Fördergut (1) auf. Die Last des Fördergutes wird über die Kette flächig auf die Kunststoffgleitschiene (Segment der Gleitschiene 3) übertragen. Nachfolgend wird die Gleitreibung zwischen den Kettengliedern und der Gleitschiene analysiert. Dazu werden ein einzelnes Kettenglied (2) und ein Segment der Gleitschiene (3) betrachtet.
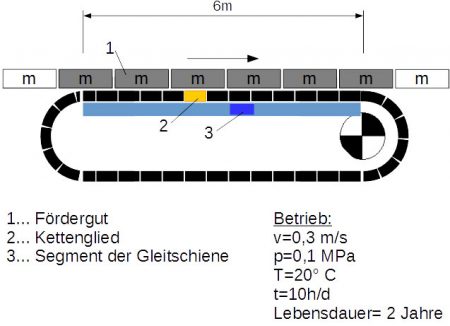
Tabelle 1: Beanspruchungsanalyse Kettenglied – Gleitschienensegment
Kettenglied | Gleitschienensegment | |
---|---|---|
Geschwindigkeit | 0,3 m/s | 0,3 m/s |
Flächenbelastung | 0,1 MPa | 0,1 MPa |
Dauer der Belastung | 20 sec, danach >20sec lastfrei | ohne Unterbrechung (Abstände zwischen Gliedern vernachlässigt) |
Umgebungstemperatur | 20° C | 20° C |
Wärmeisolierung des Reibkontakts | gering; kann durch die Umgebungsluft umströmt werden, insbesondere im Leertrum wird die Reibfläche nahezu frei belüftet | mittel bis hoch; wird nur zwischen den Kettengliedern belüftet sowie von rechts und links; Auflage der Gleitschiene auf dem Führungsprofil aus Stahl oder Aluminium wirkt sich positiv auf die Wärmeabgabe aus |
Reibfläche – Kontaktfläche | B10 mm x L20 mm | B10 mm x L20 mm |
Reibweg über die Lebensdauer | 365d x 10h x 0,5 x 3600s x 0,3 m/s = 1971 km | 365d x 10h x 3600s x 0,3 m/s = 3942 km |
Oberflächenbearbeitung | Spritzguss; Erodierstruktur | gefräst; feine Frässtruktur in Längsrichtung |
Aus der Analyse geht hervor, dass die Reibungsbeanspruchung des Kettengliedes deutlich geringer als die der Gleitschiene ist. Der Reibweg des Kettengliedes unter Last liegt bei 1971 km, der der Gleitschiene bei 3942 km. Die Gleitschiene ist beständig unter Last im Reibkontakt, während das Kettenglied im Wechsel 20 sec belastet und dann im Leertrum 20 sec quasilastfrei läuft.
4. Versuchsplanung auf Basis der Beanspruchungsanalyse
Modellversuche helfen bereits in einem frühen Entwicklungsstadium praxisnahe Versuchsergebnisse zu gewinnen und das bei geringen Kosten und Aufwand. Damit die Ergebnisse praxisnah sind und sie eine objektive Entscheidung bei der Kunststoffauswahl ermöglichen, ist folgendes Vorgehen bei der Versuchsplanung sinnvoll:
- Auswahl eines praxisnahen Versuchsprinzipes auf Basis der Analyse: Für den im Beispiel beschriebenen Fall eignet sich das Prinzip Klötzchen auf Platte mit linearoszilierender Probenbewegung. (auch geeignet: Stift-Scheibe-Prinzip)
- Probenherstellung und Oberflächengestaltung wie beim realen Bauteil: Die Proben sollten mit dem gleichen Herstellungsverfahren (Spritzgießen, Extrusion, Fräsen, etc.) wie die realen Bauteile, und insbesonderer mit der gleichen Oberflächengestalt, hergestellt werden. Kettenglied: spritzgegossene Platte mit praxisidentischer Erodiertstruktur; Gleitschiene: mit praxisidentischen Paramentern gefräst
- Probengeometrie bzw. Kontaktfläche: Die Abmessung des Klötzchens sollte nicht wesentlich von der Kontaktfläche der realen Baugruppe abweichen. Abmessung: B10 mm x L20 mm
- Probenpräparation: Die Kanten des Klötzchen sollten angefast oder verrundet werden.
- Anordnung der Bauteile: Das Bauteil, dass den größeren Reibweg zurücklegt bzw. permanent im Reibkontakt steht, entspricht dem Klötzchen. Das Bauteil, mit der geringeren Reibbeanspruchung entspricht der Platte. Kettenglied: Platte; Gleitschiene: Klötzchen
- Einstellung des Hubes: Je größer der Hub beim Klötzchen-Platte-Versuch, desto größer ist die Abweichung zwischen dem Reibweg des Klötzchens und dem Reibweg der Platte. Bei einem Hub entspricht der Reibweg des Klötzchens der Hublänge. Der Reibweg der Platte entspricht bei einem Hub der Länge des Klötzchens. Gewählter Hub: 100mm (Bei dem Stift-Scheibe-Versuch ist das Verhältnis zwischen den Reibwegen des Stiftes und der Scheibe über den Laufdurchmesser einstellbar.)
- Geschwindigkeit: =Praxisfall; v=0,3m/s
- Flächenbelastung: =Praxisfall; p=0,1 MPa
- Umgebungstemperatur: =Praxisfall; T=20° C
- Versuchsdauer: Vorauswahl: mindestens 24 h (bei v=0,3 m/s); vertiefende Untersuchungen: mindestens 168 h
Aus den gewählten Parametern ergeben sich für den Kurzzeitversuch (24 h) folgende Reibwege:
- Klötzchen: 0,3m/s x 24h x 3600s/h = 25,92km
- Platte: 25,92km / 100mm = 259.200 Hübe; 259.200 Hübe x L20mm (Klötzchen) = 5,2km
Literatur / Bibliography
[1] Czichos, H.: The priciples of systems analysis and their application to tribology, ASLE Trans. 17, 1974
[2] Weisbach, T.: Korrelationsanalyse von Tribologiekennwerten, Studienarbeit, TU-Chemnitz, Professur Fördertechnik, 2011
[3] Schüppel, M.: Analyse des Reibungs- und Verschleißverhaltens von künstlichen Gleitauflagen für Sport- und Freizeit, Abschlussarbeit, TU-Chemnitz, Professur Fördertechnik, 2011
[button label=“Download als PDF unter Veröffentlichungen“ url=“/veroeffentlichungen/“ color=“accent“ style=“stroke“]